
Hardening & A Near Death Experience
My great-grandfather was in charge of Whiteley’s during the latter part of the Victorian era. Unfortunately, he hadn’t quite got the hang of how to run a business. After becoming bored with scissor-making, he ensconced to London.
Installing himself in Claridge’s, he promptly divested himself of all the company’s money indulging in wine, women and song.
Up until 1900, all scissors were hand-forged. Whiteley’s had 12 hand forgers all very busy hammering (smithing) away. They would start with a piece of beautiful Crucible mild-carbon Sheffield steel, and work on it until it looked like a scissor blade. All screws and bolts were hand-made, too.


However, this doesn’t mean any less work for our team, as the forgings are still extremely rough! Some scissors go through 39 operations to get them from a forging to a scissor, all done by hand in our factory.
Whether it’s hand-forging or drop-forging, all scissor blades then need to be hardened. In my grandfather’s time, this was done with a chimney furnace, full of glowing coals with the blades pushed in up to the screw-hole. The furnace had air pumped through by a giant set of foot-operated bellows.
Back then, the operator of the bellows was a character called Harry Taylor, who had a hunch-back and a club foot; he would pump away with his heavy club foot wearing a special elevated boot, and always a picture of sartorial elegance in a three-piece suit and a tie.
One summer, the furnace became so hot that the window frames burst into flames as he was pumping – he didn’t stop until he had finished the batch and the fire brigade turned up! Even then, he shouted at them “I’ll just finish these”……
Eventually we switched to a ‘less hazardous’ process called salt-bath hardening, where the blades were dipped up to the screw-hole in molten cyanide salts. However, in true Whiteley style, my father once tapped his pen on the edge of the furnace absent-mindedly, and later chewed the end of it while at his desk. After he woke up in hospital – a very narrow escape! – we switched to a non-toxic, tastier type of hardening salt, so he could tap the furnace without having to worry about such pesky things as dropping dead. We still use that salt today.
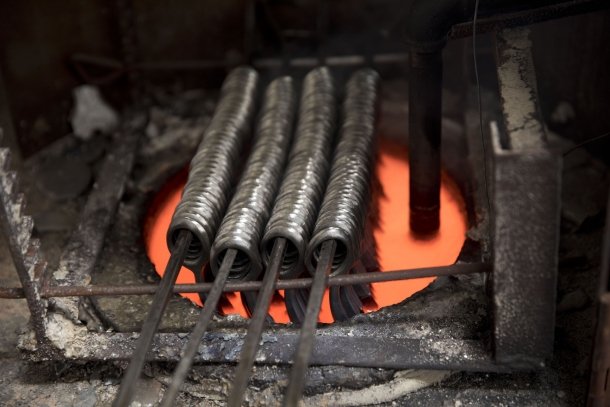